On March 3rd, Construction Equipment Technology Innovation Forum under the theme of “technology leads the development and innovation drives the future” is held in Wuhan. Fifty-six experts and scholars in China from the fields of research, design, manufacturing and management of construction equipment and bridges are present to share the technological innovation experience of construction equipment and talk about the dream of developing equipment in China in the new era.
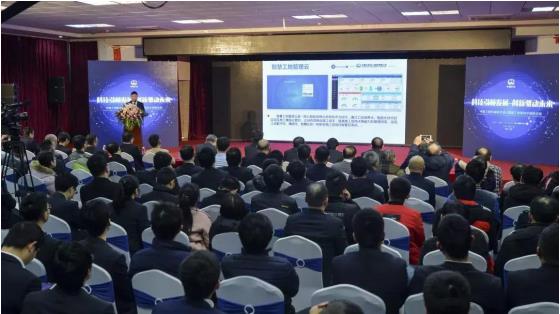
This forum is one of the commemorative activities for the 40th anniversary of the establishment of China Railway Engineering Machinery Research & Design Institute (“the Institute”), China Railway Science and Industry Group Co., Ltd. under CRHIC. In addition to this forum, the Institute has also launched a photo exhibition for the 40-year development, a symposium of retired experts and technical backbones and other activities, in an attempt to recall the hardship of equipment manufacturing in China, and to explore the innovative development direction of construction equipment in a new era.
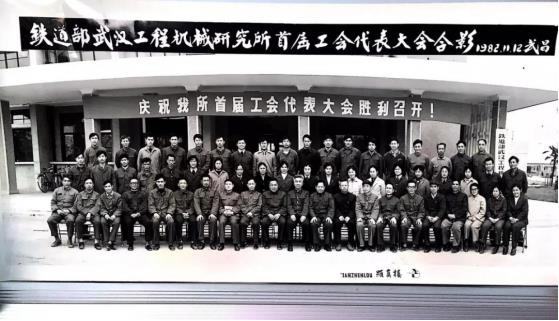
▲ Group Photo of the 1st Congress of Trade Unions of Wuhan Engineering Machinery Institute of Railway Ministry in 1982
On the occasion of the reform and opening-up and the National Science and Technology Conference of 1978, the Ministry of Railways assembled national elites in the field of railway engineering machinery research and manufacturing to establish Wuhan Engineering Machinery Institute of Railway Ministry (the predecessor of the Institute), the only institution specializing in railway engineering machinery research and manufacturing at the beginning of 1979, in order to rapidly improve the level of national railway construction mechanization.
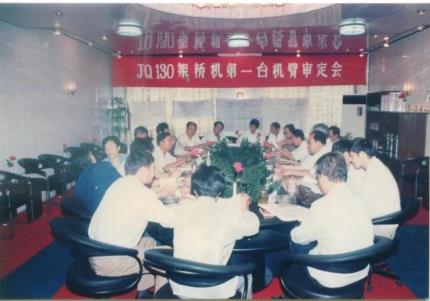
▲Developing JQ130, a new generation of bridge erecting machine in 1990, which was successfully applied in the girder erecting operation of Beijing-Kowloon Railway in 1994 to realize the one-time erection of girder in the air.
Over the past 40 years, the Institute has always stayed true to its original aspiration and ranked first for dozens of items in China. It has been evaluated as a national high-tech enterprise, a railway construction machinery standardized technology enterprise, and a China railway construction equipment technology research and development center. It is included in the national team of railway construction equipment research and development in China. The Institute possesses an integrated capability that covers research, design, manufacturing and service of railway construction equipment, has more than 20 technologies that fill the domestic blank and 11 technologies that are far ahead in the world, and leads the industry in the fields of special construction equipment development, construction equipment safety assessment, and remote operation & maintenance technology of railway and rail transit. It is known as the “home to high-speed rail construction artifacts”.
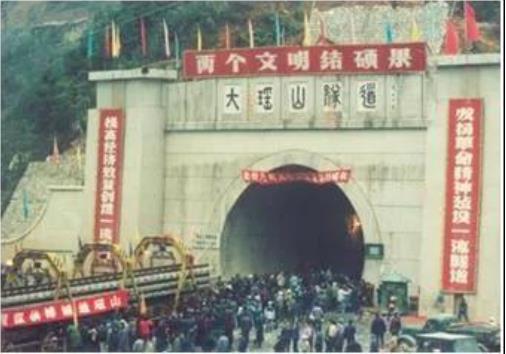
▲In November 1981, major technical forces carrying out scientific experiments at Dayaoshan Double-Line Electrified Tunnel, the longest tunnel in China, to serve the on-site construction
In the history of China’s high-speed railway construction, the Institute has contributed to three major breakthroughs in box girder manufacturing technologies of high-speed railway bridges. The first breakthrough was made in 2000, during which the building technology for box girder with a weight of 600 tons and a length of 24 meters was applied in the construction of Qinhuangdao-Shenyang Dedicated Passenger Railway, the first quasi-high speed railway in China. The second breakthrough was made in 2006, during which the building technology for box girder with a weight of 900 tons and a length of 32 meters was applied in the construction of Hefei-Nanjing Railway. Since then, the technology has been widely used in the construction of Beijing-Shanghai High Speed Railway, Guangzhou-Wuhan High Speed Railway, Shanghai-Kunming High Speed Railway and other high speed railways. The third breakthrough was made in the construction of the Zhengzhou-Jinan High Speed Railway, during which the building technology for box girder with a weight of 1,000 tons and a length of 40 meters was applied.
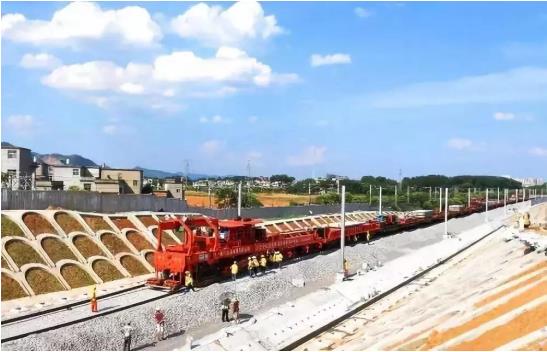
▲The Institute’s CCPG500 high speed railway seamless track laying machine operating in Kenya